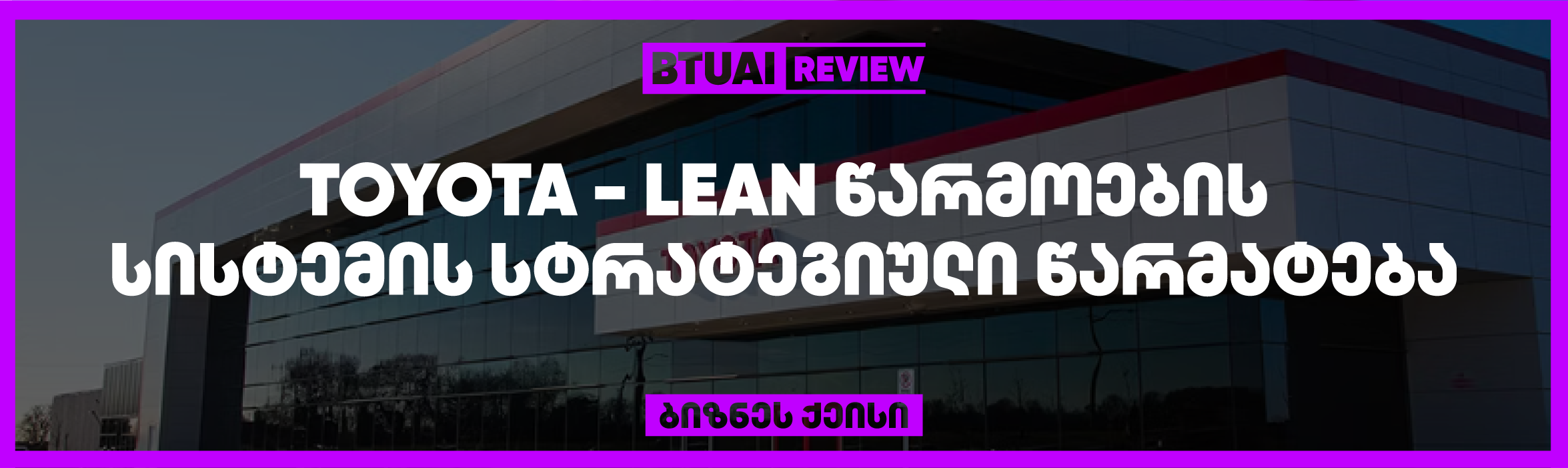
Toyota-მ Lean წარმოების სისტემა დანერგა, რათა მაქსიმალურად გაემარტივებინა ოპერაციული პროცესი და შეემცირებინა ნარჩენები, რაც გახდა გლობალური ავტომობილების ინდუსტრიის რევოლუციური სტრატეგია. კომპანიის ეფექტურობა და მოქნილობა მნიშვნელოვნად გაიზარდა ამ სისტემის მეშვეობით.
Toyota-ს Lean წარმოების სისტემა (TPS) გახდა ერთ-ერთი ყველაზე გავლენიანი და წარმატებული სტრატეგიული ინიციატივა ავტომობილების წარმოების ინდუსტრიაში. ეს სისტემა არა მხოლოდ დაეხმარა Toyota-ს, რომ წარმოების პროცესი უფრო ეფექტური გაეხადა, არამედ საფუძველი ჩაუყარა კომპანიის გლობალურ ზრდასა და ავტომობილების ინდუსტრიაში ლიდერობას. Lean სისტემამ მენეჯმენტის სფეროში ახალი სტანდარტი დაამკვიდრა და მრავალი ინდუსტრიისთვის მისაბაძი მაგალითი გახდა.
პრობლემა:
1950-იან წლებში Toyota იბრძოდა ავტომობილების წარმოების ინდუსტრიაში თავისი პოზიციის გამყარებისთვის, განსაკუთრებით აშშ-ის ბაზარზე, რომელზეც კონკურენცია იყო მაღალი და ამერიკული ავტომწარმოებლები (როგორიცაა Ford და GM) დომინირებდნენ. Toyota-ს არ ჰქონდა საკმარისი რესურსები და ფინანსური სიმძლავრე, რომ ტრადიციულად კონკურენცია გაეწია ამერიკული კომპანიებისთვის მასიური წარმოების სფეროში. ამასთანავე, კომპანიას სჭირდებოდა უფრო მოქნილი და ეფექტური წარმოების სისტემა, რომელიც მინიმალური დანაკარგებითა და მაღალი ხარისხით გამოირჩეოდა.
გადაჭრის სტრატეგია:
Toyota-ს ერთ-ერთმა ხელმძღვანელმა, ტაიიჩი ონომ, დაიწყო ახალი საწარმოო სისტემის შექმნა, რომელიც აერთიანებდა რამდენიმე სტრატეგიულ პრინციპს. მისი მიზანი იყო წარმოების მაქსიმალური ოპტიმიზაცია და დანაკარგების მინიმალიზაცია. შედეგად შეიქმნა Lean წარმოების სისტემა, რომელსაც ორი ძირითადი პრინციპი ჰქონდა:
- „Just-in-Time“ (JIT) წარმოება:
Toyota-მ დანერგა „Just-in-Time“ წარმოების სისტემა, რომლის მიხედვითაც კომპანიის ნაწილები და მასალები დროულად მიეწოდებოდა წარმოებას მხოლოდ მაშინ, როდესაც საჭირო იყო. ამან შეამცირა ზედმეტი მარაგი და ნარჩენები, რაც კომპანიას საშუალებას აძლევდა წარმოების ხარჯები მკვეთრად შეემცირებინა და მომხმარებლის მოთხოვნებზე სწრაფად ეპასუხა. - კაიზენის პრინციპი:
კაიზენის (უკვე არსებული პროცესების მუდმივი გაუმჯობესება) ფილოსოფია გახდა Toyota-ს საწარმოო სტრატეგიის ერთ-ერთი ცენტრალური ელემენტი. ამ მიდგომის მიხედვით, კომპანიის თანამშრომლები მუდმივად ეძებდნენ გზებს სამუშაო პროცესებისა და წარმოების ოპტიმიზაციისთვის. კაიზენის პრინციპი გულისხმობდა გუნდის ყოველი წევრის ჩართულობას პროცესების გაუმჯობესებაში, რაც კომპანიას დაეხმარა მომხმარებლისთვის უკეთესი ხარისხის პროდუქციის მიწოდებასა და ხარჯების კონტროლში. - „Heijunka“ (წარმოებისა და ოპერაციების გათანაბრება):
Toyota-მ ასევე დანერგა Heijunka-ს მეთოდი, რომელიც გულისხმობდა წარმოების გათანაბრებასა და ოპერაციების მუდმივ ჰარმონიაში მოქცევას. ეს ხელს უწყობდა წარმოების პროცესში არასტაბილურობის შემცირებასა და კომპანიის უფრო მოქნილ მუშაობას სხვადასხვა ტიპის პროდუქტებზე.
შედეგები:
Lean წარმოების სისტემის დანერგვამ Toyota-ს გლობალურ ბაზარზე წარმატება მოუტანა. 1970-იან წლებში, როდესაც ნავთობის კრიზისი დაიწყო, Toyota-მ აჩვენა თავისი წარმოების მოქნილობა და ეფექტურობა, რითაც შეძლო ბაზარზე თავისი წილის სწრაფი გაზრდა. უფრო ეკონომიური და მაღალი ხარისხის ავტომობილები მომხმარებლების ყურადღებას იპყრობდნენ, განსაკუთრებით იმ დროს, როცა ამერიკული კომპანიები არ იყვნენ მზად სწრაფად ადაპტირებისთვის.
Lean წარმოების სისტემა არა მხოლოდ გააძლიერა Toyota-ს გლობალური პოზიციები, არამედ გახდა მწარმოებლობის ახალი სტანდარტი, რომელსაც სხვა კომპანიებიც აქტიურად ითვისებდნენ სხვადასხვა ინდუსტრიაში. Toyota-მ Lean სისტემის წყალობით შეძლო, რომ მისი წარმოების ხარჯები და დანაკარგები მინიმუმამდე დაეყვანა, ხოლო ხარისხის კონტროლი და მომხმარებელთან მჭიდრო ურთიერთობა გაეუმჯობესებინა.
მარკეტინგული სწავლება:
Toyota-ს Lean წარმოების სისტემა არის ერთ-ერთი საუკეთესო მაგალითი იმისა, თუ როგორ შეუძლია სტრატეგიულ მენეჯმენტსა და წარმოების ოპტიმიზაციას არა მხოლოდ კომპანიის შიდა პროცესების გაუმჯობესება, არამედ გლობალური ბაზრის დომინაცია. Lean სისტემა დღესაც გამოიყენება მსოფლიოს მრავალ კომპანიაში და ითვლება საწარმოო ინდუსტრიის ერთ-ერთ ყველაზე მნიშვნელოვან სტრატეგიულ მიღწევად.
წყაროები:
- Harvard Business Review
- The Wall Street Journal
- Forbes